Exele TopView assists Flakeboard in Energy Savings
Flakeboard Co. Ltd. is an industry leader in the production of quality composite wood panels. Using lumber industry by-products and under-utilized wood species once landfilled or burned as waste by forestry operators or sawmills, Flakeboard manufactures a variety of particleboard, medium-density fibreboard (MDF), and FIBREX® thin high-density MDF.
Flakeboard needed a system to facilitate the analysis and allocation of energy costs for each mill. They turned to their Electrical Systems Coordinator, Pat Burke, whose job included Energy Management for the whole Flakeboard Corporation. “We knew how much we were spending on energy overall, but it was deemed important to be able to understand the breakdown of the energy used by each of the mill’s production lines to determine a cost per unit.” said Burke.
Flakeboard decided to implement a long-term energy-savings program. This involved an Energy audit, implementation design, and the use of Energy Management software which includes Exele TopView for real-time monitoring and notification.
Audit
The first step was an Energy Management Information System (EMIS) Audit. The Audit was necessary to determine the potential energy savings and to estimate the funds required to implement a full EMIS. That audit revealed that $1 million in energy savings could be achieved over a 3-year evaluation period and this was a key factor in getting management’s approval to move forward.
Implementation
Using the data from the EMIS Audit an EMIS implementation plan was developed which included: a process to establish baseline data, selecting the appropriate meters for the acquisition of energy usage data, and development of a software specification for monitoring and employee training programs.
Flakeboard’s EMIS used energy account centers (EACs). Each of their 120 energy account centers includes energy-using (electricity, oil, water, compressed air) production processes at each of the mill’s various processing and finishing lines where meaningful energy use is concentrated.
Forty Electrical meters were added as well as meters for oil, gas, water, and compressed air at the St Stephen Site. The energy meters data is combined with production rates, temperatures, and other significant system variables to enable the EMIS software to calculate the performance of each energy account center to target.
Data Analysis & Reporting
Incorporating all of the production, environmental, and metered data together is RtEMIS from RtTECH Software, Inc. The software built to the specifications developed in Flakeboard’s implementation plan shows the detailed energy targets for each of the mill line’s EACs in near “Real Time” and identifies savings and losses in both dollars and energy units.
The RtEMIS software is used to show the day-to-day energy consumption and the percentage of the target reached as well as the cost and cumulative savings.
Verifying that energy usage data is being communicated is critical to the calculations and historical analysis. “One of the major factors in choosing the RtEMIS system over the others that we looked at was their ability to monitor input data,” said Burke. “The other systems could go ‘flatline’ for hours or days without anyone ever knowing that they stopped tracking usage.” The RtEMIS software incorporated EXELE TopView, a data monitoring and notification software package capable of monitoring the data flow from all the various meters and other sources. TopView interfaces directly with the energy and process data and notifies the appropriate personnel if it detects any abnormalities, such as a non-functioning meter, in the data being transmitted.
TopView also handles the reporting functions. Each morning the system automatically sends a status report on all communication devices. Additionally, each HMI screen in the facility receives messages when a process has exceeded its preset threshold. Messages are also emailed to the appropriate managers.
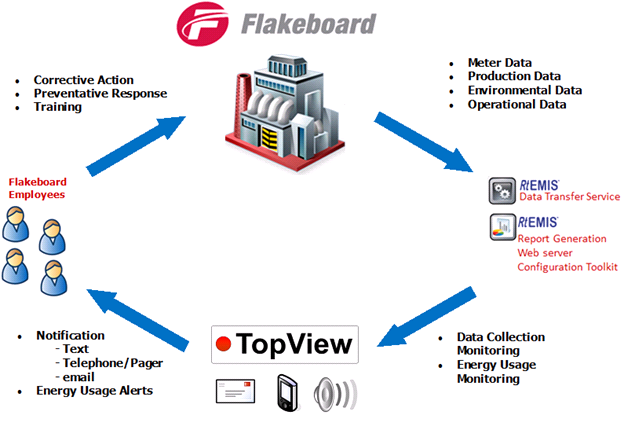
Results
The system immediately identified opportunities where fans, compressed air, and lighting systems were left on even when the production wasn’t running. The staff has become more aware of the potential energy savings and has changed their work habits as a result.
Each production line now has energy target levels set for full production and zero production, or idle, status and usage are measured against these targets. Status reports on peak levels for each energy account center illustrate the reduction in energy consumption and allow for new, lower targets to be set as energy savings are realized.
Flakeboard has experienced savings in energy costs of $260,000 in a 12 month period and continues to work to improve efficiency. Flakeboard was recently recognized for its efforts in energy conservation at the biennial Energy Conference co-hosted by Natural Resources Canada (NRCan). At their conference, the Canadian Industry Program for Energy Conservation (CIPEC) honored Flakeboard with the CIPEC Leadership Award for making a significant and innovative contribution to energy efficiency in the monitoring and targeting category. Read more about Flakeboard’s efforts in the CIPEC 2012 Annual Report.
Ready to get started?
Contact Exele today or download a free trial version of TopView